Specialized machines
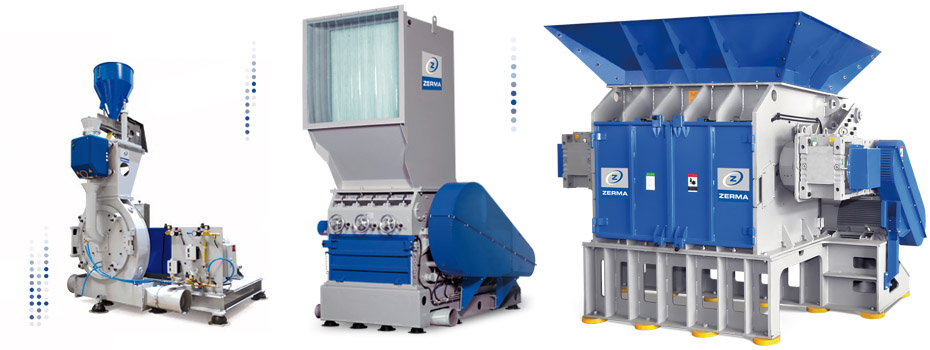
The right solution for today’s recycling needs
ZERMA offers the following machine series:
ZCS - Shredder/Granulator combination
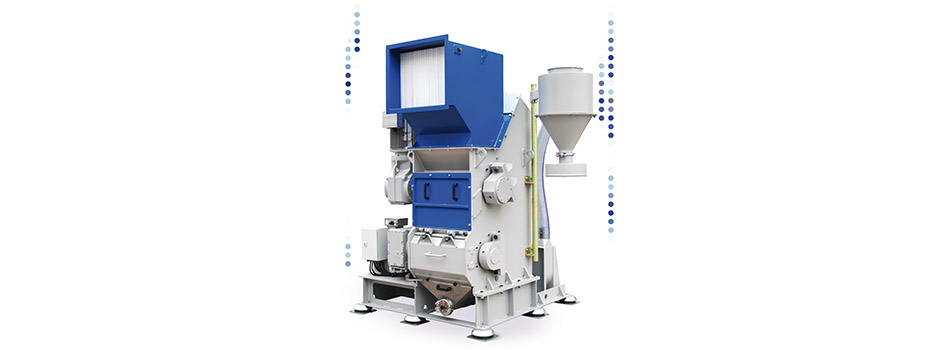
The ZCS size reduction system combines a shredder with a granulator in a single space saving system for the processing of production waste. The shredder part is equipped with a 400 mm diameter E rotor using ZERMAs proven knife and knife holder design, driven by a high-torque gear drive, which in comparison to a direct drive also handles tougher input materials well. The large material hopper and the powerful horizontal pusher allow processing of voluminous as well as heavier parts. The lower part of the system consists of a 3-blade granulator rotor based on the GST series. The shredder and granulator are matched to work together ideally and in conjunction with an advanced control system ensure smooth reliable operation.
The ZCS system has been developed mainly focused on blow- and injection molding, but can be used in other fields as well.
Due to the compact design it is ideal for in house recycling applications. The closed system reduces the risk of contamination in the output material compared to a traditional two stage system.
- Compact space saving design
- Low noise emission
- Versatile size reduction concept
- Flexible discharge options
PM - Pulverizers
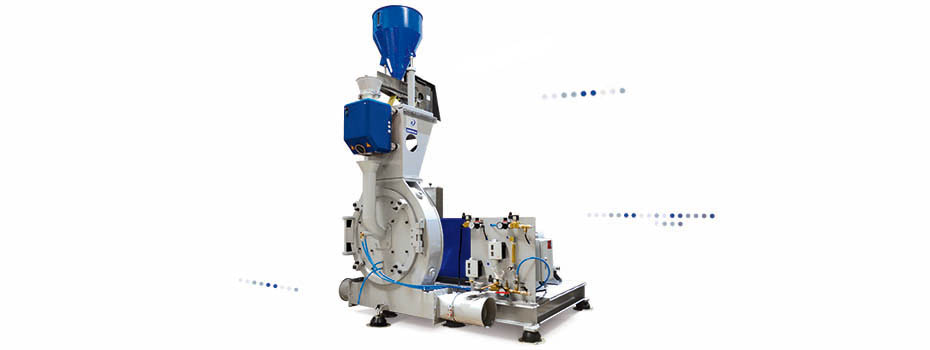
The disc pulverizers of the PM series are available with disc diameter from 300 to 800 mm. These pulverizers are high speed, precision grinders for the processing of medium hard, impact resistant and friable materials. The material to be pulverized is introduced through the centre of a vertically fixed grinding disc which is mounted concentrically with an identical high speed rotating disc. Centrifugal force carries the material through the grinding area and the resulting powder is collected with a blower and cyclone system. Depending on the application the machines can be equipped with one piece grinding discs or grinding segments.
One of the main fields of use for the ZERMA PM Pulverizers is the pulverization of PVC regrind in pipe and profile recycling. Working in line with a shredder and granulator to have a balanced and efficient system to handle in house production wast
- Simple adjustment of cutting gap
- Choice of discs or segments
- Low drive power
- High throughput
- Innovative efficient design
- Wide range of accessories
- Easy temperature control
ZHM - hammer mill for brittle materials
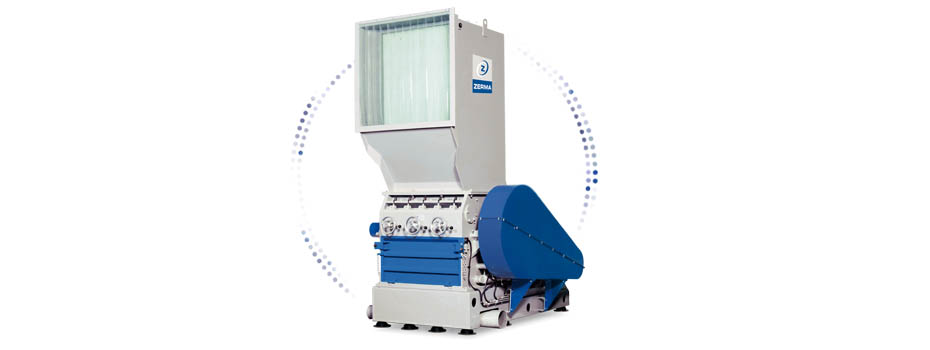
The ZHM series of hammer mills feature heavy duty rotors ranging from 600 to 800 mm diameter and widths between 800 and 1200 mm directly driven via Vs.-belts. The fixed rotor tools, heavy counter knives and several rows of pre breakers create high impact powers and throughput rates while make tool changes fast and easy. All tools and wear parts are manufactured from highly wear resistant steel. The housing design inherits the advantages of the proven GSH granulator design, such as the diagonally divided cutting chamber and hydraulic screen cradle for easy maintenance and servicing. Various screen sizes allow for a wide range of applications and degrees of disintegration.
Traditionally hammer mills are used in the wood industry to generate sawdust, but proved usable in other industries as well as a size reduction solution for brittle materials such as glass, bakelite and later on plastic such as PVC. In the PVC industry it is still used to separate used window profiles from their metallic reinforcement and fittings
The main purpose for the ZERMA ZHM today is the processing of electronic waste, such as whole computers, white goods and ICBs. The main advantage in these processes lies in its insensitivity to contamination and abrasive materials while being able to achieve a rather small output material. Through the high degree of disintegration it is possible to achieve good separation results in the following processes.
- Suitable for highly contaminated or abrasive materials
- Fixed hammer design and Heavy Duty design
- High throughput rates
- Easy tool change and maintenance
- Good disintegration of mixed input materials
ZTS/ZTTS - Fine shredders
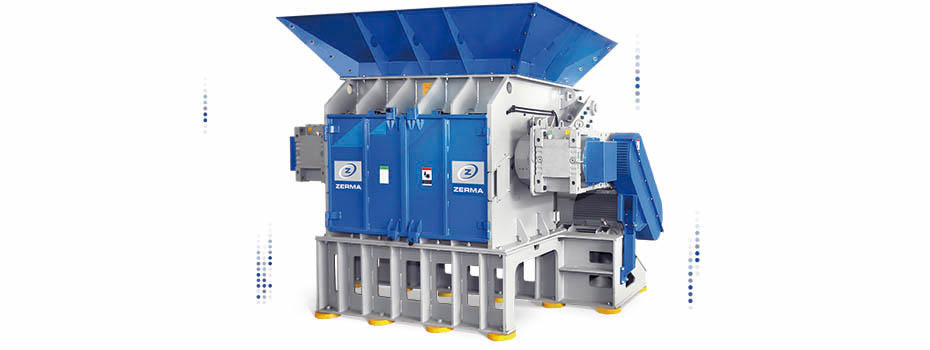
The ZTS and ZTTS single shaft shredders are specially designed for the processing of complete or pre shred tires. Both machines machines feature a 750 mm diameter rotor ranging in width from 1500 to 3000 mm with oversized outboard bearings and twin gear drives. The tangential infeed ensures a optimal feeding of the input materials while eliminating the need for a hydraulic feeding system. All tire shredders are equipped with a complete wear package including hard facing, special knives and wear plates made from highly wear resistant steel. The two model ranges differ in the amount of stator knives and the screen sizes used. The modular design makes it easy to integrate either machine into existing installations.
The twin rows of stator knives and screen in the ZTTS enable it to take the tire shreds down to a any required size > 20 mm. The unique machine design combined with the variable cutting gap create an optimal separation of rubber and steel fractions when the machine is used with a 20 mm screen. Therefore steel can be removed easily in the following process with magnetic separation equipment. Beside tires the machines are also used in the conditioning of RDF and other alternative fuel applications.
- Single big diameter rotor (750 mm)
- Proprietary knife design and material
- Variable knife gap to improve separation of steel and rubber
- Compact Heavy Duty design+ High throughput rates
- Fast and easy tool change and maintenance