ZERMA size reduction solutions
Solutions for inline recycling
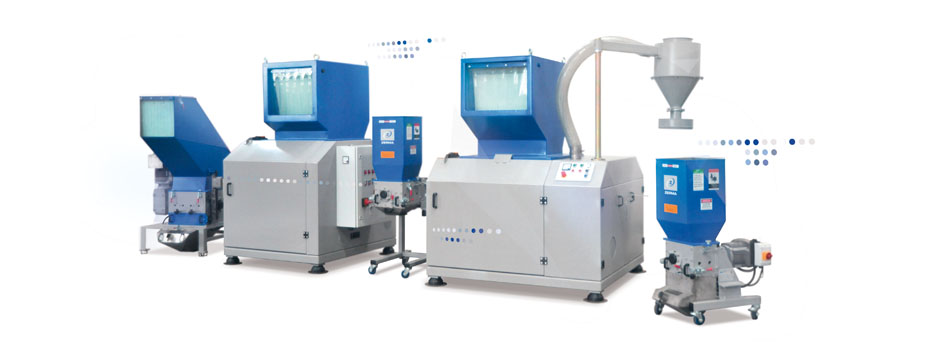
The right machine
for Inline-Recycling
Granulation and size reduction of plastics, e.g. scrap from blow and injection moulding or extrusion processes, requires a lot of know how and experience. ZERMA has a long history in the design and implementation of size reduction equipment and offers a product portfolio which is as wide as the spectrum of materials that need to be processed. ZERMA granulators in the GSL, GST and GSC series are specially designed for in house recycling applications in line with the production machinery. The regrind can be directly reintroduced into the production process or stored in a central silo. The compact size and low noise emission make these machines ideally suited for in-house scrap.
- Machines can be easily integrated into the production process
- Low noise level
- Quick and simple maintenance while complying with global safety requirements
- Customizable to fit specific needs
ZERMA offers the following machine series for use in in-house applications:
- GSL
- Slow Speed Granulators to directly grind runners and sprues from the injection machine
- GST
- Soundproofed granulators featuring a very aggressive tangential infeed and cutting chamber
- GSC
- Soundproofed compact granulators suited for a wide variety of inline tasks
- GSE
- Same as GSC series, but without soundproofed housing
- ZCS
- Space saving shredder/granulator combination
- Consistent final product
- Reduced fine particles
- Low heat generation
- Reduced noise emission
- Small footprint
- Easy maintenance
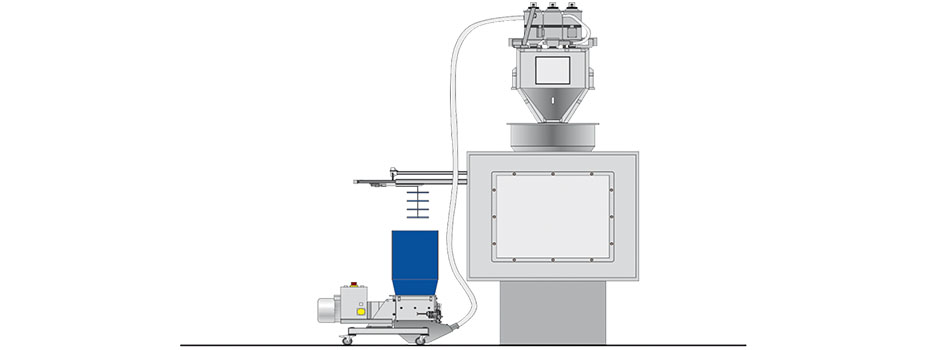
GSL granulator
next to injection molding machine
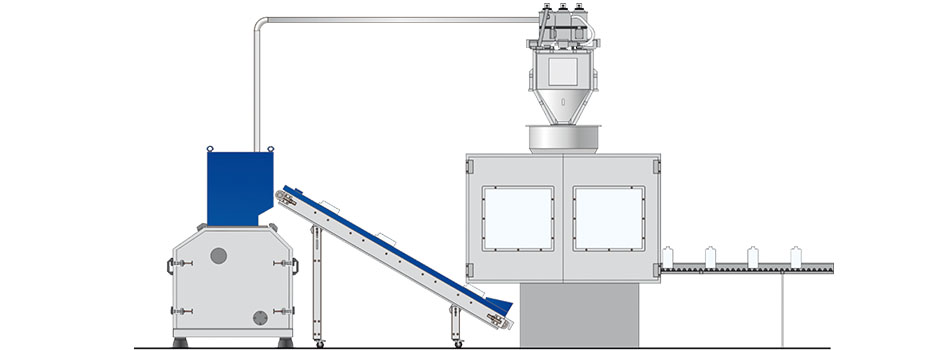
Granulator for
tops and tails
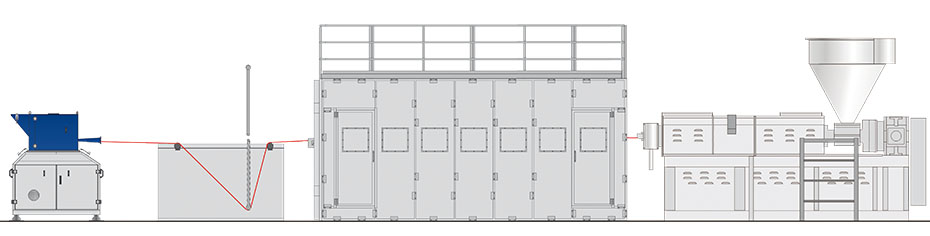
Online grinding of thermoforming skeleton
Recycling solutions
Overview:
In the plastic industry it started pretty late compared to the much longer existing scrap metal and paper and card board collectors and recyclers. Also the achieved recycling rate at around 25% is much lower than in the 2 longer existing areas. This on the other hand makes the field very interesting as there's a lot of growth potential especially with raising oil prices. One thing which makes plastic recycling more and more difficult is the vast amount of different plastics and their blend with at least the same amount of possible additives and fillers.
This industry is traditionally divided into two groups:
Contractors:
Getting waste from the plastic manufacturing industry to process it for an agreed price into re-usable products like re-grinds and/or compounds. As in this case the source and the user of the recycled material are the same and the recycled material goes straight back into the production.
Independent recyclers:
Buying waste from all kind of sources and selling it to 3rd parties. In this case the recycled materials usually are used for a lower grade product as the buyer often does not know the source and real material specification.
Common products to be processed in both fields are usually rejected parts, runners, lumps and purgings. The input materials can be very different in their physical properties as well as in their dimension and shapes. This makes it very important to choose the right machine for each application not just to match the required throughputs but also to be able to handle the parts given.
Our solution:
ZERMA offers for this field a wide range of shredders, granulators and pulverizers. To little parts like handle tiny runners to thick-walled pipes and turn them into chips, flakes, granules or even powders. We are one of the very few recycling machinery makers to have the whole spectrum for this under one roof and all made by ZERMA, no OEMs. This gives us the advantage to put together just the right set up to get your job done the best and most economical way. Together with our auxiliaries equipment like belt conveyors, separators and air conveying systems we can realize complete recycling systems to create a valuable product from virtually any initial infeed material.
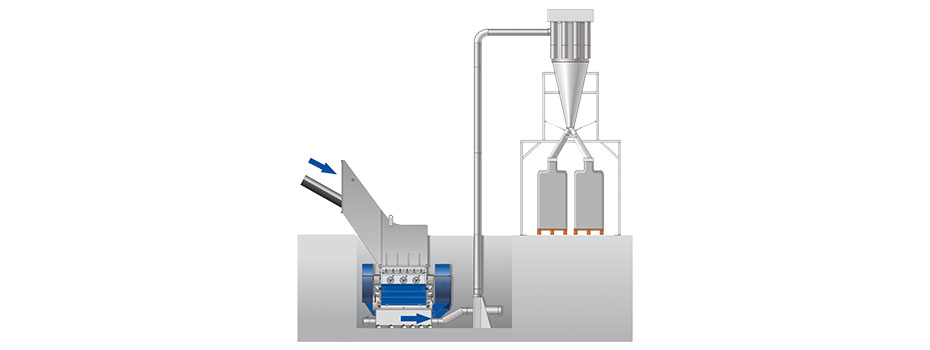
GSH granulator
placed in a pit to feed long parts
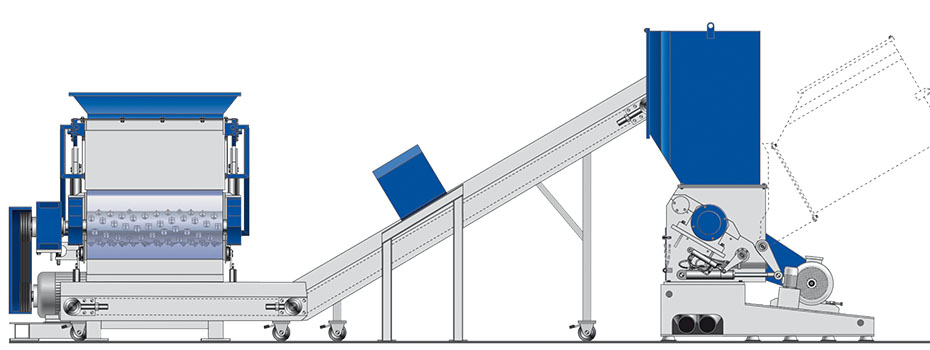
Two stage recycling system
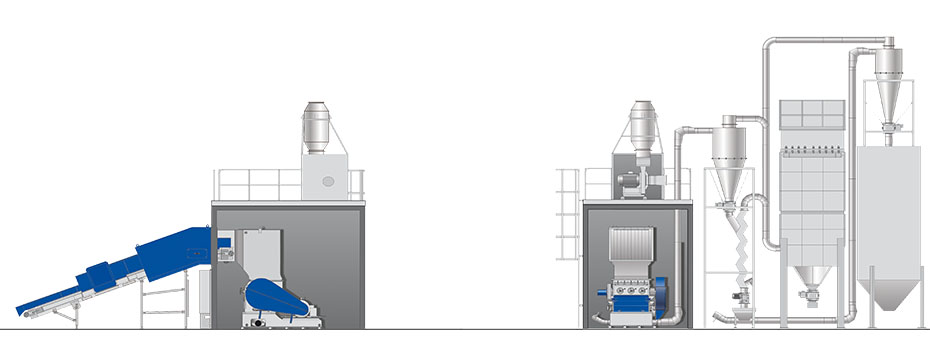
Granulator in separate soundproofed room
Post consumer recycling solutions
General information:
As the latest way of recycling the post consumer recycling is also one of the fastest growing markets, caused by shortage of resources and soaring energy costs. On one side new products are made from daily waste we produce, best example here the recycling of PET bottles into yarns and fibres for the textile industry and on the other side refused products with good caloric values are turned into fuels for boilers, cement kilns, power plants and so on.
In the case of turning waste into new raw materials the plastic stream is usually pre-sorted by either the consumer himself, through waste sorting plants or through independent waste collectors as it is often the case in developing countries. As the source of such materials is usually spread all over a country there are normally lots of small and medium sized collection centres to guide the waste stream into the final processing facilities. To reduce transport cost it arrives there mostly baled or sometimes pre-shred. Only then it is when the final, mostly manual, sorting is done; different kinds and grades of materials, different colours etc. From this point onwards the recycling is then more or less automated and big varieties of input materials as the already mentioned PET-bottles, PE-films and bottles, PVC window frames, PP from toys and household ware, ABS computer and TV housings and lots of more, are turned into re-usable granules, powders, flakes and compounds. Depending on the grade of purity they are turned then into high valuable products like new bottles, yarns or less valuable things like flower pots and garbage bags.
When waste is turned into energy then it is usually not only the plastic fraction but all other things with caloric value as well, wood, biomass, tires etc. In this case the purpose of shredding the input material is to get a homogeneous mix, which is easier to handle, to store and to feed into the next step. For this kind of operation it is necessary that shredding is as efficient as possible so that the energy balance is right and the operation is economical. Because of that a shredder should always run on the biggest screen possible to get maximum output at rated current.
The biggest problem in such an energetic recycling is the high level of contaminants as the boilers usually don't care about mineral and metallic particle. But for the lifetime of the cutting tools and the wear and tear of the shredder itself a clean as possible input material is necessary.
Our solution:
For both cases ZERMA is able to provide just the right equipment to make your operation as profitable as possible. Our shredders are tough built and with a large range of machines and drive options we can achieve output capacities just as you require. And if you wish all in wear resistant executions.
Rough sizing with our shredder range, granulating with our granulator range or even micronizing with our pulverizers; all from on hand. Further we do all the other things needed to complete the set up, like conveyors, feeders, separators, blowers, cyclones etc.
Advantages:
- Sturdy design
- We can offer machines for all steps of the size reduction either as a complete line or as replacements for existing systems
- High market share in this field
- Low investment costs against highly efficient machines
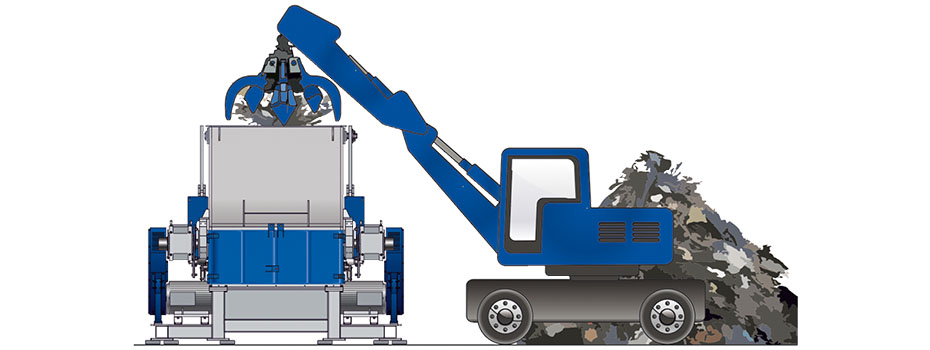
Large shredder for MSW shredding
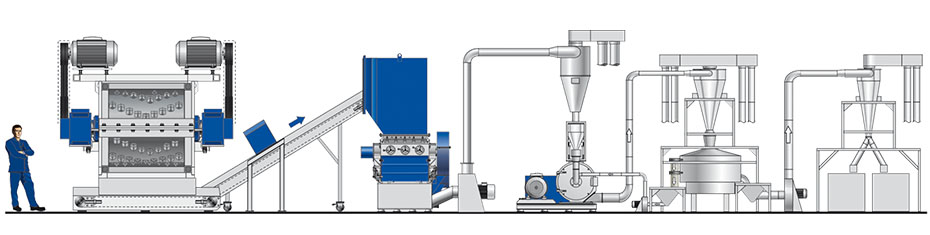
Three stage recycling system for pipes
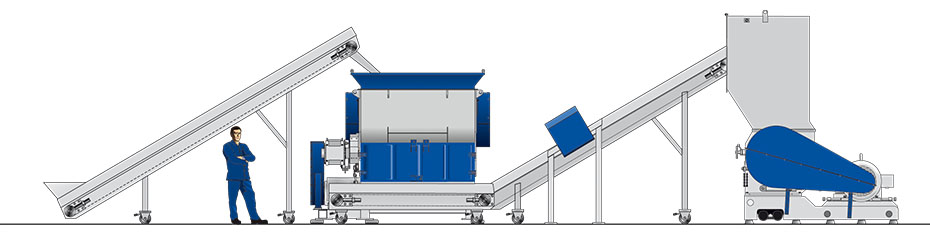
Two stage size reduction
with metal detection